Porosity in Welding: Identifying Common Issues and Implementing Ideal Practices for Avoidance
Porosity in welding is a pervasive concern that frequently goes undetected until it causes considerable issues with the stability of welds. This typical flaw can jeopardize the strength and durability of welded structures, presenting safety risks and leading to expensive rework. By comprehending the origin of porosity and executing reliable avoidance approaches, welders can dramatically enhance the high quality and reliability of their welds. In this conversation, we will check out the vital factors adding to porosity formation, examine its harmful impacts on weld performance, and review the ideal methods that can be embraced to minimize porosity event in welding procedures.
Typical Causes of Porosity
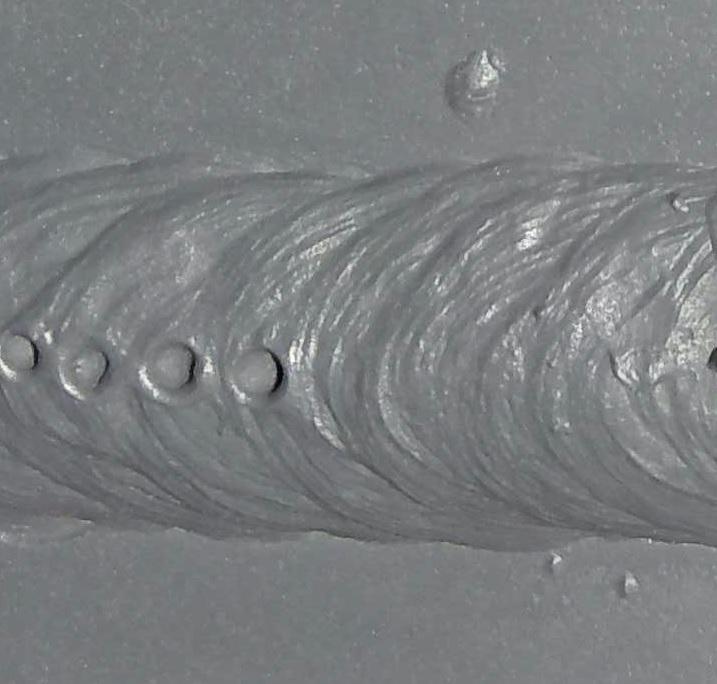
Using filthy or wet filler products can present contaminations into the weld, contributing to porosity concerns. To minimize these typical reasons of porosity, thorough cleaning of base steels, correct protecting gas selection, and adherence to ideal welding specifications are essential techniques in accomplishing high-grade, porosity-free welds.
Impact of Porosity on Weld High Quality

The presence of porosity in welding can dramatically compromise the architectural honesty and mechanical residential properties of bonded joints. Porosity develops voids within the weld metal, damaging its total strength and load-bearing capability.
Among the key repercussions of porosity is a reduction in the weld's ductility and durability. Welds with high porosity degrees tend to display reduced influence toughness and minimized ability to flaw plastically before fracturing. This can be specifically worrying in applications where the welded elements go through vibrant or cyclic loading problems. Porosity can hamper the weld's capacity to effectively transfer pressures, leading to premature weld failure and prospective safety risks in critical frameworks. What is Porosity.
Best Practices for Porosity Avoidance
To enhance the structural stability and high quality of bonded joints, what specific measures can be executed to decrease the event of porosity throughout the welding process? Making use of the appropriate welding method for the details product being bonded, such as changing the welding angle and anchor weapon position, can additionally protect against porosity. Routine examination of welds and prompt removal of any type of problems recognized throughout the welding process are necessary methods to prevent porosity and produce high-quality welds.
Importance of Proper Welding Techniques
Carrying out appropriate welding strategies is extremely important in making sure the architectural integrity and quality of bonded joints, developing upon the structure of reliable porosity avoidance steps. Too much warm can lead to raised porosity due to the entrapment of gases in the weld swimming pool. Furthermore, making use of the appropriate welding parameters, such as voltage, current, and take a trip rate, is essential for accomplishing sound welds with very little porosity.
In addition, the option of welding process, whether it be MIG, TIG, or stick welding, ought to straighten with the particular requirements of the task to make certain optimal results. Appropriate cleaning and prep work of the base steel, along with selecting the right filler material, are also vital parts of proficient welding methods. By adhering to these finest practices, welders can lessen the danger of porosity formation and create top notch, structurally audio welds.

Evaluating and Top Quality Control Measures
Testing treatments are crucial to spot and stop porosity in welding, ensuring important site the strength and toughness of the last item. Non-destructive screening visit this page approaches such as ultrasonic screening, radiographic testing, and aesthetic examination are typically utilized to identify potential defects like porosity.
Post-weld evaluations, on the other hand, examine the last weld for any problems, including porosity, and verify that it meets defined requirements. Implementing an extensive quality control plan that includes comprehensive testing procedures and examinations is vital to lowering porosity problems and making sure the general top quality of welded joints.
Conclusion
Finally, porosity in welding can be a common problem that influences the top quality of welds. By identifying the typical sources of porosity and carrying out finest techniques for prevention, such as appropriate welding methods and screening measures, welders can make certain top quality and reliable welds. It is necessary to prioritize prevention techniques to minimize the occurrence of porosity and preserve the stability of bonded structures.